Frequently Asked Questions about the VeriTape® LTO Cartridge Quality Analyzer
Q&A With a VeriTape Engineer
Q: I had a back-up failure and the drive displayed "media error". I scanned the cartridge and the VeriScore was 76. Any comment?
A: One of the most misleading messages is the “media error” message on an LTO drive. The message simply means that the drive encountered an error condition from which it cannot recover. It may be due to defective media, but this is only one of many error possibilities and is actually quite an unlikely one. A “media error” message usually means that the drive needs maintenance, and there is in fact no problem with the cartridge. According to media vendors, as many as 90% of perfectly good cartridges are being returned. Differentiating between drive and media problems is a well-known problem. The VeriTape software (Version 2.0.0.4 or higher) solves this problem. In addition to rating the cartridges, the drives are also rated on the same scale. Drives that require maintenance are easily detected. Now you can have your tape drives serviced before they generate those confusing or misleading messages.
Q: "I noticed that the current reader covers up to LTO-4. Will the hardware of the analyzer be compatible with later versions of LTO?"
David Walton, Systems & Network Support, British Geological Survey, Keyworth, UK
A: The hardware of the VeriTape analyzer will be compatible with future LTO generations. We will modify the software as required.
Q: How can I justify the expenditure?
Identifying bad or marginal cartridges before problems happen can prevent costly failures to complete the job (called job "abends" for abnormal end of jobs by Imation). The cost of a job abend and rerun can be quite high. Imation Corp (www.imation.com) estimates the cost of a job rerun for an average data center to be about $1,000. In the figure below Imation projects the cost as a function of job reruns for 3 abends/week and for 7 abends/week. According to Imation’s cost analysis, your savings would pay for VeriTape in less than a week. (See WhitePaper_IMN_Recertified_Media.pdf, page 3)
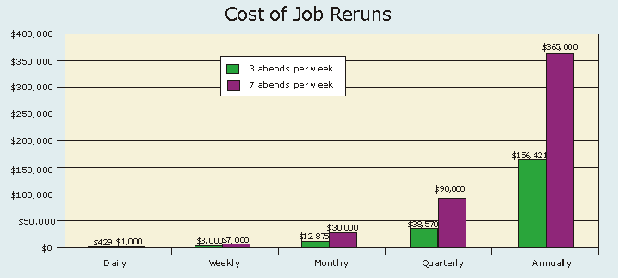
Q: We don’t have any problems in our data center. Why would I need your product?
A: Our product helps you to maintain this valuable ‘no problems’ status. Sometimes it takes just one problem, a failure, for example, to restore a lost file from a back-up tape to lose that ‘our data center is great’ label.
Q: "...I have great interest in Veritape. Its seems a powerful tool in evaluating the performance of each cartridge and help to find out the problem cartridges. However, you know, there are many possibility of the root causes, it may be the problem of cartridge, or may be the problem of the tape drive, or even the setting of the overall system."
Keneth Lau - Fujifilm distributor, Hong Kong (website, email)
A: We agree that a backup or restore problem may be caused by a number of factors. The current version of VeriTape software (1.4.2.0) gives an overall score for each cartridge. Our next release of software, which will be free to all customers, will automatically analyze and rate each tape drive in addition to scoring each cartridge. This software will be available in the next few months.
Q: VeriTape displays the statistical numbers from the CM, which shows the past performance of the cartridge. How does this relate to the future performance of the cartridge?
A: The quality of data cartridge diminishes over time. By monitoring the statistical data you can spot problem cartridges early and remove them before they cause problems. For cartridges, past performance is a quite reliable predictor of future performance.
Q: How long does it take to scan a cartridge?
A: About 3 seconds.
Q: I have many cartridges that I need to scan. What do I have to do to tell the VeriTape software that a cartridge is ready to be scanned?
A: VeriTape has an “auto scan” option. When this option is enabled the software detects the presence of a cartridge without user intervention. All you have to do is place the cartridge on the scanner. When the scan is complete, remove the cartridge and put the next cartridge on the scanner.
Q: I would like to save the scan data for each cartridge in a file. Do I have to type in a file name for each cartridge?
A: No. When using the“auto save” option, VeriTape will automatically save the file, using the cartridge serial number as part of the file name. Again, all you have to do is place the cartridge on the scanner. When the scan is complete, simply remove the cartridge and put the next cartridge on the scanner. VeriTape does the rest, including writing the data to a file.
Q: When should I scan my cartridges?
A: We recommend that cartridges be scanned periodically. This way the progression of a cartridge can be monitored.
Q: How do I know if a cartridge is getting bad?
A: The easiest way to judge cartridge quality is to monitor its VeriScore. A dropping VeriScore shows that the cartridge should be retired.
Q: How is VeriScore calculated?
A: We use all relevant data, such as error statistic, number of bytes written and read, number of mounts, and age of cartridge to calculate VeriScore. The parameters are weighted according to their importance on the cartridge quality. Error counts are weighted more heavily than age of the cartridge, for example. Some types of errors, such as recovered write errors, are weighted more heavily than others and are less severe than a non-recovered read error. More recent errors are more important than older errors.
Q: We are sending cartridges periodically to off-site storage facilities. Should I scan the cartridges before sending them out?
A: Absolutely. It is very important that the best cartridges are selected for off-site storage. Although most storage facilities take excellent care of your cartridges, it may be years before a restore from one of the cartridges is required. The tape drive on which the cartridge is read will be most likely not the drive that wrote the cartridge. The restoring drive may even be of a later technology generation. You want the highest margins you can get to avoid an unpleasant restore failure.
Q: I scanned a new cartridge, but VeriTape shows that data has been written to the cartridge. Did I inadvertently buy a used cartridge?
A: Not necessarily. The manufacturer may test some new cartridges prior to shipping. In this case VeriTape discloses the statistical data of the tests. Typically the test data written is less than 5% of the cartridge capacity. If VeriTape shows that the cartridge has a high number of mounts and a lot of data has been written to the cartridge, you have bought a used cartridge. You should contact your vendor and request an explanation.
Q: I scanned a new cartridge and VeriTape reveled that the cartridge had been tested by the vendor. The number of errors that occurred during the test is high. What is the criterion for rejecting a cartridge?
A: This is a question for the manufacturer of the cartridge. We reviewed several scan files of new cartridges that our customers sent to us. In some cases we shared their surprise that the manufacturer sold a cartridge with high errors data.
Q: I bought a reconditioned cartridge, but VeriTape shows zero cartridge mounts and zero data written to the cartridge. How is this possible?
A: The cartridge memory chip has been set to zero by the company that ‘reconditioned’ the cartridge. They have a very good reason for doing this. They want to hide the history of the cartridge from you. Don’t buy from this vendor! After all, would you buy a used car if the odometer had been set to zero?
Q: Do you have any patents?
A: We have applied for patent protection for several technologies used in VeriTape.
If you have any question that isn't addressed here or a recommendation on how this product could be improved, please email Data Devices and we will help you.
